Emerald green to cinnamon brown, smooth to the touch, and often adorned with fine decoration – lead-glazed pottery quickly catches the archaeologists’ eye among the hundreds of sherds found in archaeological contexts. As this type of pottery was only produced in the late Hellenistic and early Imperial periods (ca. 50 BCE to 50 CE), it is quite a rare find. All the more striking was a considerable concentration of pottery fragments with green glaze discovered at the intraurban periphery of Pergamon, more precisely at the steep and rocky northern East Slope. These finds, however, were not the usual fine drinking vessels that have been unearthed in the past, but mostly rather large and coarser vessels and objects used to produce this delicate ware (fig. 1).
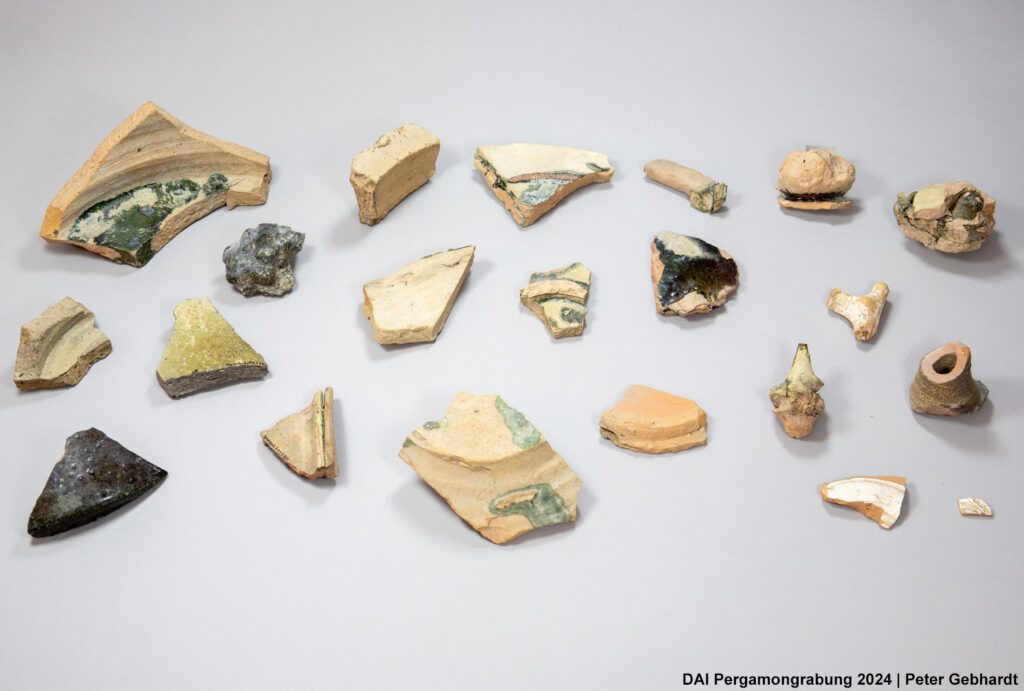
The production of lead-glazed ware required numerous raw materials, such as clay, water, wood, and metal scraps, as well as a careful stacking technique in the kiln. After thorough examination of misfired vessels, saucers, and stacking devices, several sequences of the firing process may be reconstructed: Large bowls or platters formed the base on which the vessels were stacked, while simultaneously catching the glaze that was turning liquid at high temperatures. Ring or tube stilts were placed into these saucers, onto which the vessels were stacked. In comparison with production waste from Perge (southwestern Türkiye), it can be assumed that tripod stilts were placed on top of the tube stilts in Pergamon as well (fig. 2). Another more space-consuming stacking variant were lid or plate-shaped stacking devices, between which vessels were loaded into the kiln (fig. 3).
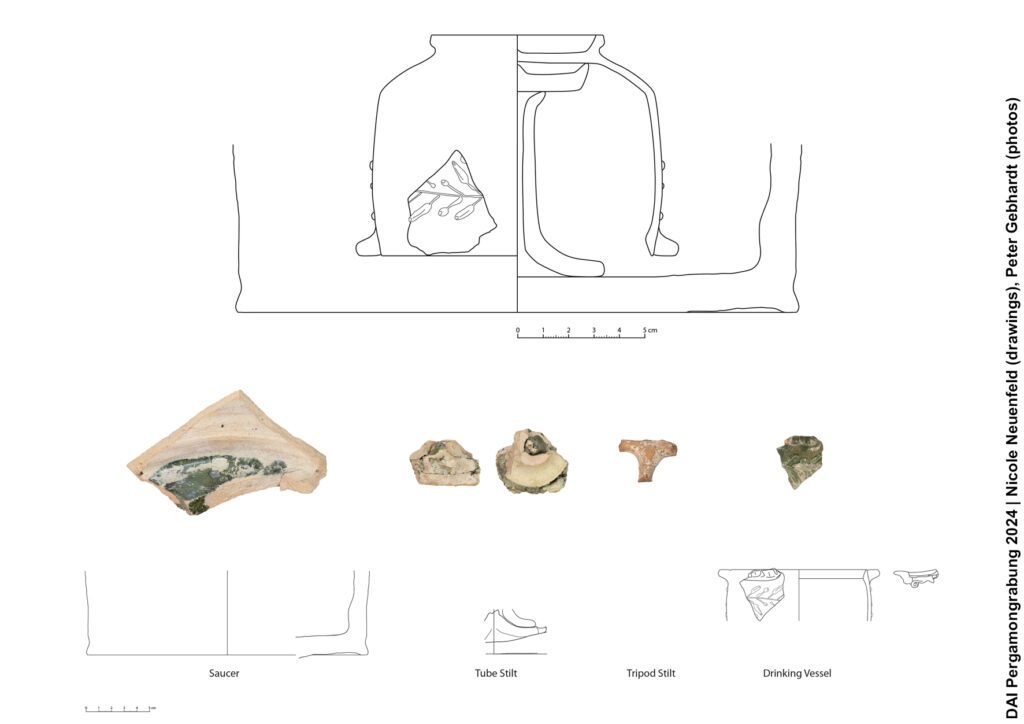
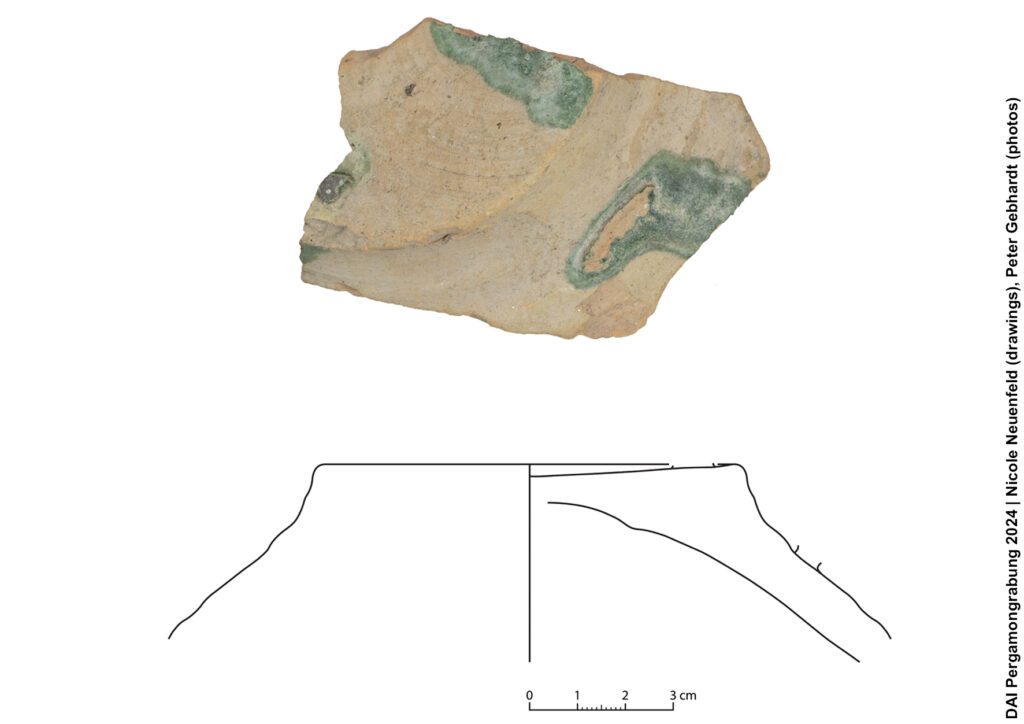
Evidently, not every firing process went according to plan. The blistered surface of a skyphos is evidence of an incorrect firing temperature or composition of the glaze (fig. 4). Cracks in the saucers also reveal that the material consumption was relatively extensive. To counteract this, attempts were made to seal and cover some cracks with raw clay after the last firing (fig. 5). Some firing processes even resulted in stacking devices sticking to the saucer due to the hardened glaze. One piece shows several tube stilts stacked on top of each other in order to use the saucer again (fig. 6).
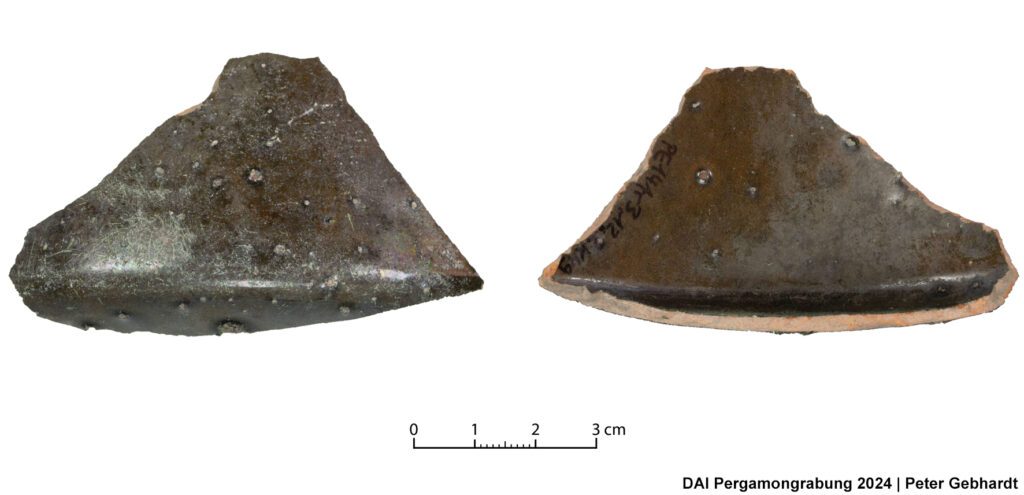
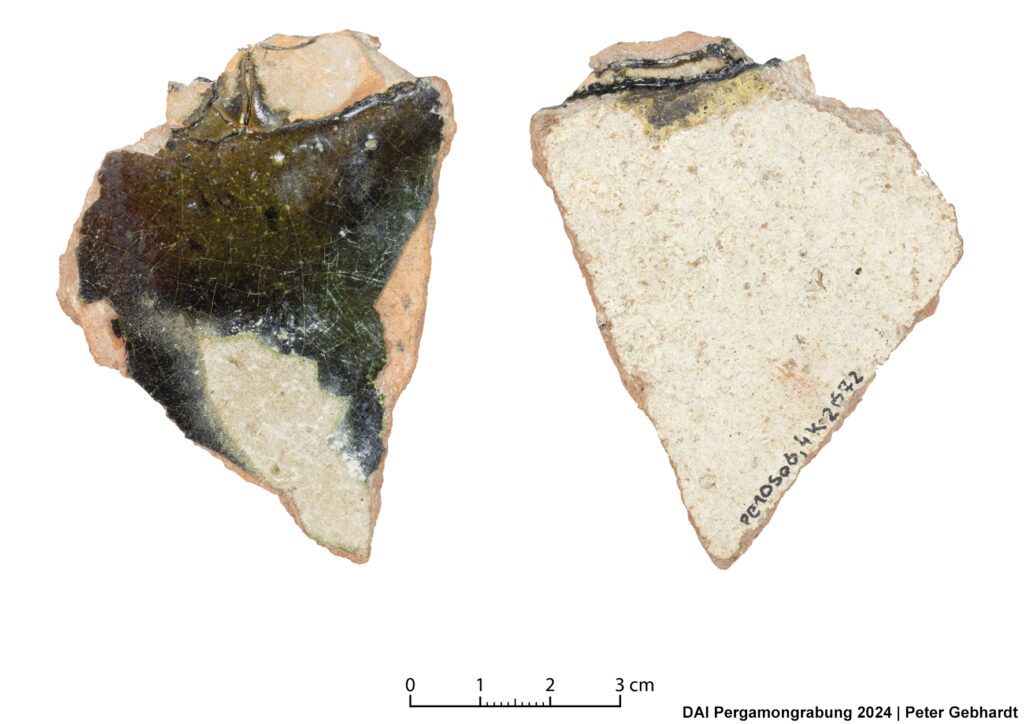
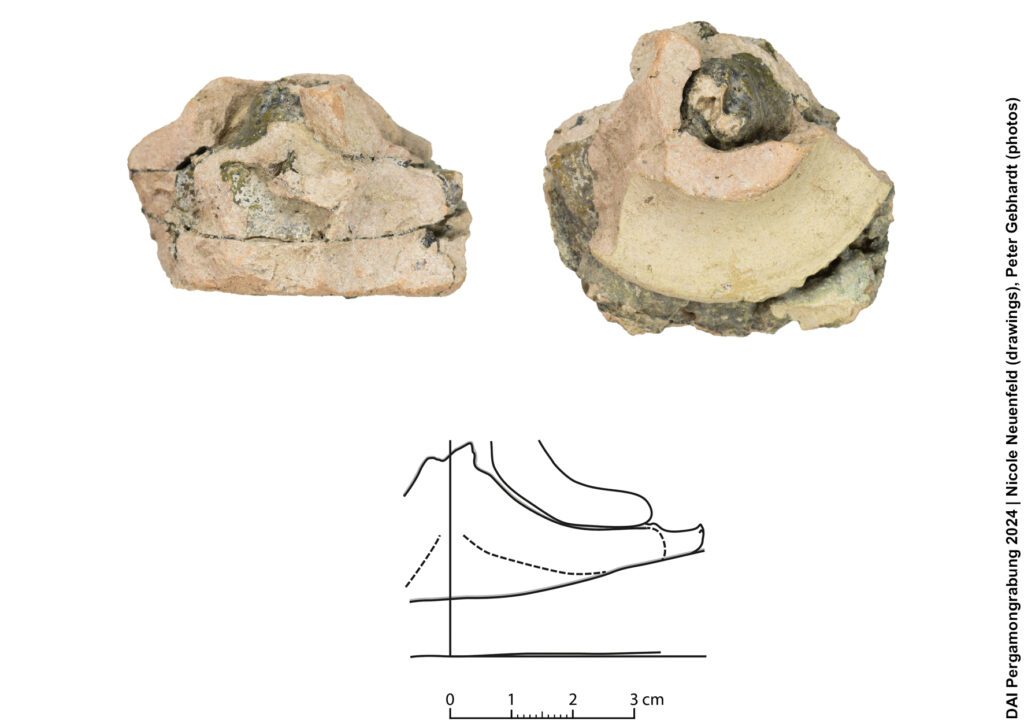
The production waste presented here shows a shimmering dimension of the long-standing and highly diversified pottery production in Pergamon and its microregion. Until now, the production of lead-glazed pottery within the city was merely assumed, but could not be proven. Although no production site or kilns were discovered and the production waste was found in a metre-high sequence of rubbish layers in the abandoned so-called Banqueting House (fig. 7), the production site must have been located within the Eumenian city extension. This is supported by the fact that the waste was unearthed below a trafficable road from which the rubbish could be dumped with a cart.
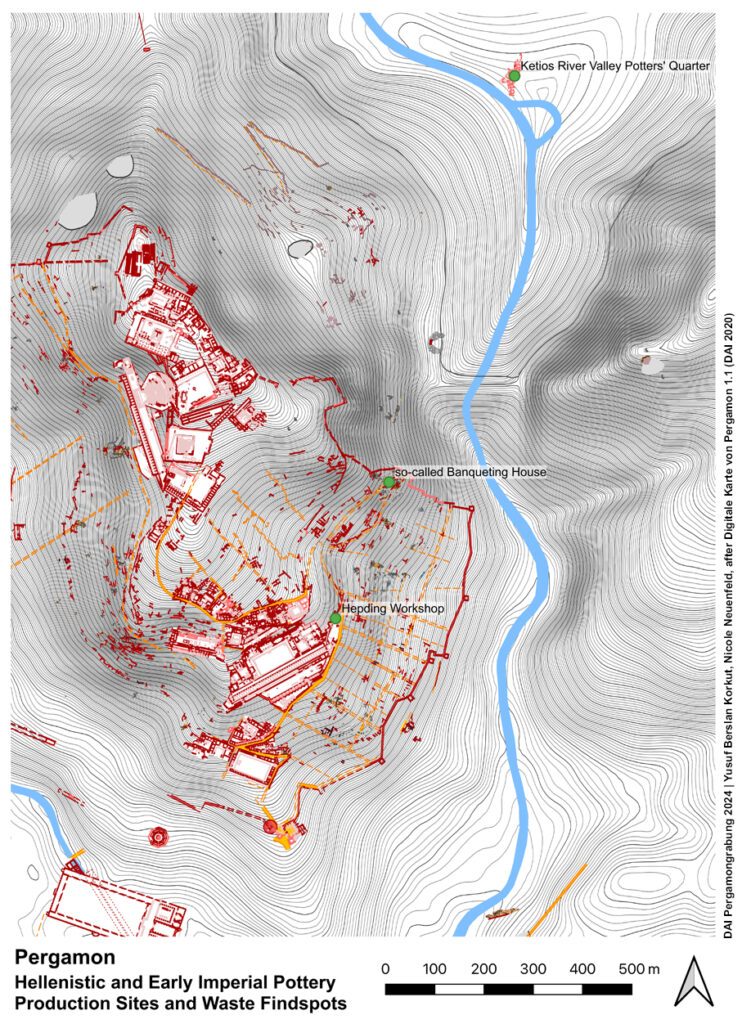
The discovery of production waste within the city walls calls for a reconsideration of the local urban production infrastructure: With the so-called Hepding Workshop in the area of the Hellenistic gymnasium, a small-sized workshop is already known, and will certainly not have been the last one to be discovered within the Eumenian city expansion. The connection of both this kiln and the northern East Slope to the large pottery production centre in the Ketios River Valley must have been an important location factor, enabling highly specialised production thanks to fast and simple transport routes of possibly pre-processed material.
Not only the integration into existing local production infrastructure enabled small-scale production, but the urban development itself may be regarded as a driver of innovation. By enlarging the urban area from 21 to 91 hectares under Eumenes II in the early 2nd century BCE, the city expansion created, on the one hand, space for new infrastructure and workshops, and, on the other hand, breeding ground for the emergence and exchange of new ideas. Other production waste such as crucibles for metal works found in the survey on the East Slope speaks of a vibrant and lively quarter with a variety of production facilities. The use of metal scraps for the production of the raw glaze should be mentioned here for the interplay of workshops, however, the interpersonal exchange should not be overlooked. Rare hybrid vessels, such as thin-walled pottery with a lead-glazed outer surface (fig. 8), are striking examples of the fusion of new trends and trial and error processes.
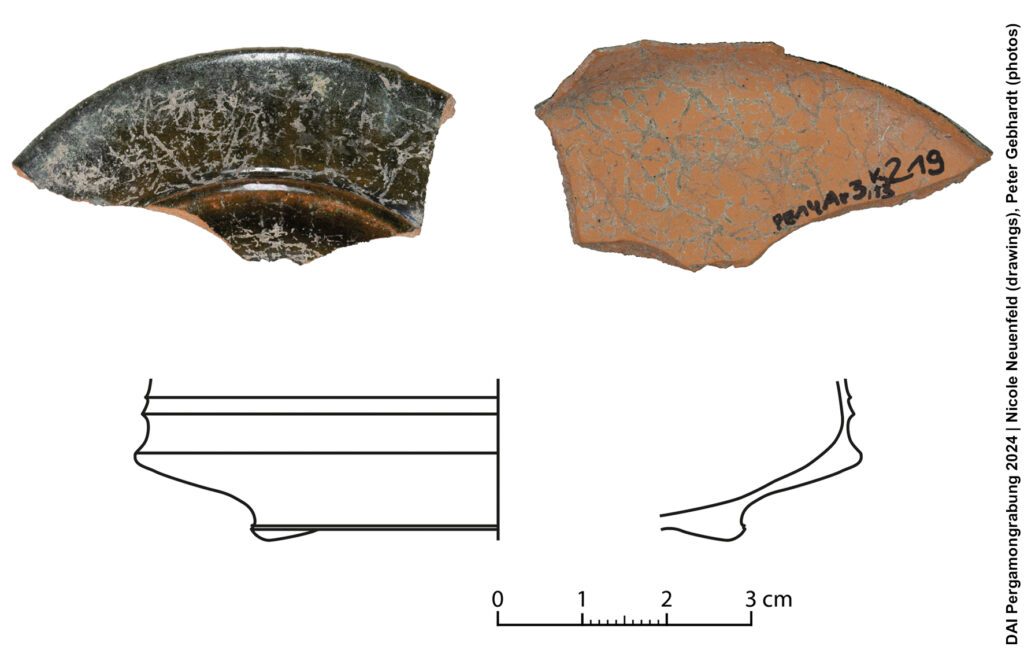
Find by find, the synthesis of urban and microregional pottery production reveals a coherent picture and provides us with information about ancient resource exploitation, craftsmanship and innovation processes. In the case of lead-glazed pottery, questions continue to arise about the emergence and short production period: What was the relationship between the urban Pergamene production and the close-by lead-glazed pottery production sites of Pitane (Çandarlı) and Mytilene (Lesbos/Greece)? Was the use of resources for production too extensive for the output? Was the highly specialised production too susceptible to disruptive factors such as supply chain complications? Or were new trends in glass and pottery simply more popular and caused an imminent end to the production of lead-glazed pottery? The numerous ongoing projects on the Pergamene pottery region harbour hopes that these questions will soon be answered.
– – –